JEPCO successfully led the planning and execution of a critical Programmable Logic Controller (PLC) upgrade for a major midstream company’s pump station facility.
The project began with the development of a comprehensive execution plan that addressed all technical and operational aspects of the upgrade, ensuring minimal disruption to ongoing operations. This plan detailed each phase of the upgrade process, including risk mitigation strategies, resource planning, and coordination with the client’s operations team.
Once approved, the JEPCO team implemented the plan, which included:
- PLC Code Reconfiguration:
Refactoring and updating the existing PLC logic to align with the latest process control standards and operational requirements.
- Loop Checks:
Comprehensive verification of all control loops, ensuring accurate signal routing and functional response from field instrumentation through the SCADA system.
- Network Infrastructure Modifications:
Upgrades to the Ethernet network topology, including new hardware installations, improved segmentation, enhanced communication reliability between system components.
- PLC-to-PLC Communications Configuration & Checkout:
Configuration of secure and reliable communication channels between multiple PLCs within the station, ensuring seamless data exchange and system synchronization.
Throughout the project, JEPCO maintained a strong focus on safety, system integrity, and efficient execution. The upgrade was completed on time and within budget, resulting in enhanced control system reliability, improved diagnostics, and greater operational visibility for the client.
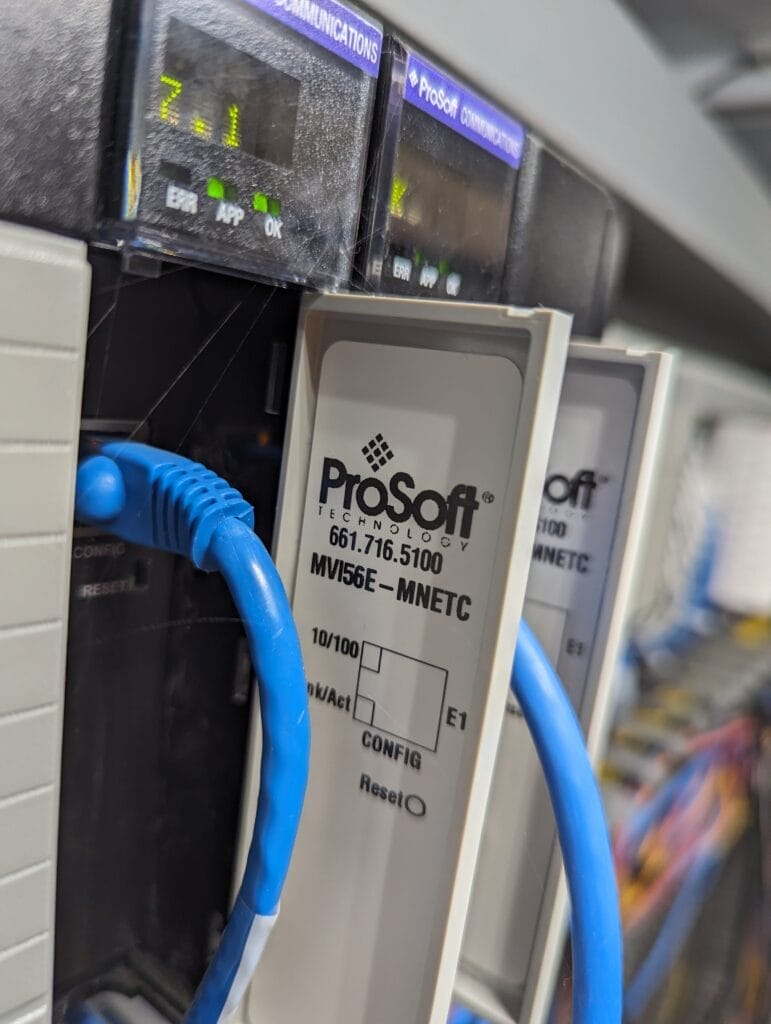
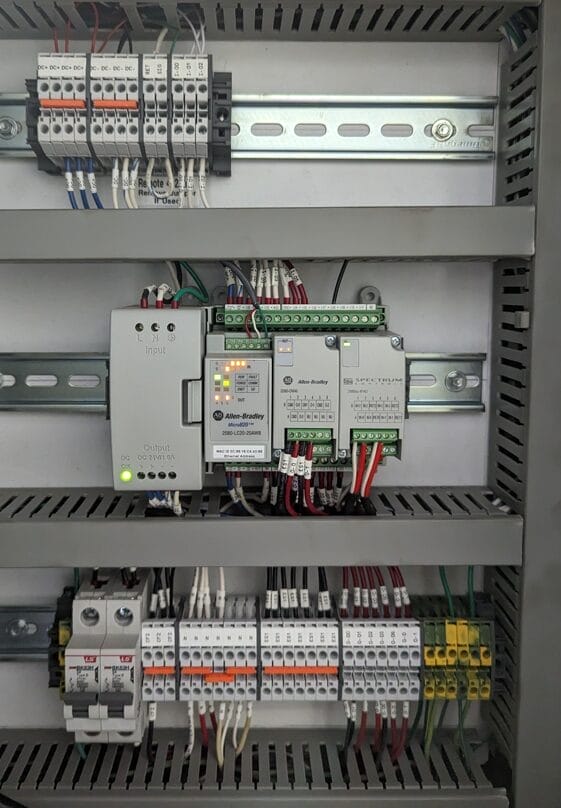