How Fixing A Chemical Imbalance Saved a Client $500,000
Problem: Injecting neutralizing amine is used to control overhead (OVHD) corrosion by neutralizing HCl at the water dew point. This is traditionally done by controlling OVHD accumulator water pH within a range of 5.5-6.5. The OVHD accumulator water contains both strong acids such as HCl and H2SO4 and weak acids such as CO2, H2S, SO3 and SO2 species. In hot dew point water, only two elements/compounds will dissolve: chloride gas and neutralizer vapor. When the two enter dew point water in equal concentration (1:1 stoichiometry), the resulting pH is 6.1. The accumulator water can also contain other amine species, such as ammonia and tramp amines, from crude oil H2S scavengers. If injecting neutralizer to control dew point aqueous chloride corrosion is done strictly by monitoring OVHD accumulator pH, either underfeed or overfeed of neutralizer can occur. Underfeed will cause significant corrosion risk and overfeed will increase cost and salting risk.
Operational Impact: A chemical vendor was controlling OVHD neutralizer injection rate strictly based on accumulator pH without taking into consideration the composition of the species in the water. As a result, gross overfeed of neutralizer occurred because the accumulator water had formed a buffered environment. The neutralizer was being overfed at 2-3 times the actual water dew point/chloride requirement to control the accumulator water within range.
Solution/Action Plan: The JEPCO team worked with both the refiner and vendor to educate them on how to determine the correct neutralizer injection rates for the chloride and water dew point conditions. JEPCO introduced the concept of strong and weak acid lab testing to calculate the correct neutralizer injection rate to minimize aqueous corrosion at the dew point.
Deliverables: The JEPCO team developed an Excel worksheet that the crude unit engineer could use to calculate the correct neutralizer dosage based on the OVHD accumulator water chemistry and atmospheric tower operating conditions.
Results: Since introducing neutralizer injection based on dew point/chloride requirements, the daily neutralizer injecting rate has decreased from an average of 150 gpd to approximately 70 gpd. The graph below shows the impact of controlling neutralizer injection rate based on strong acids and chlorides.
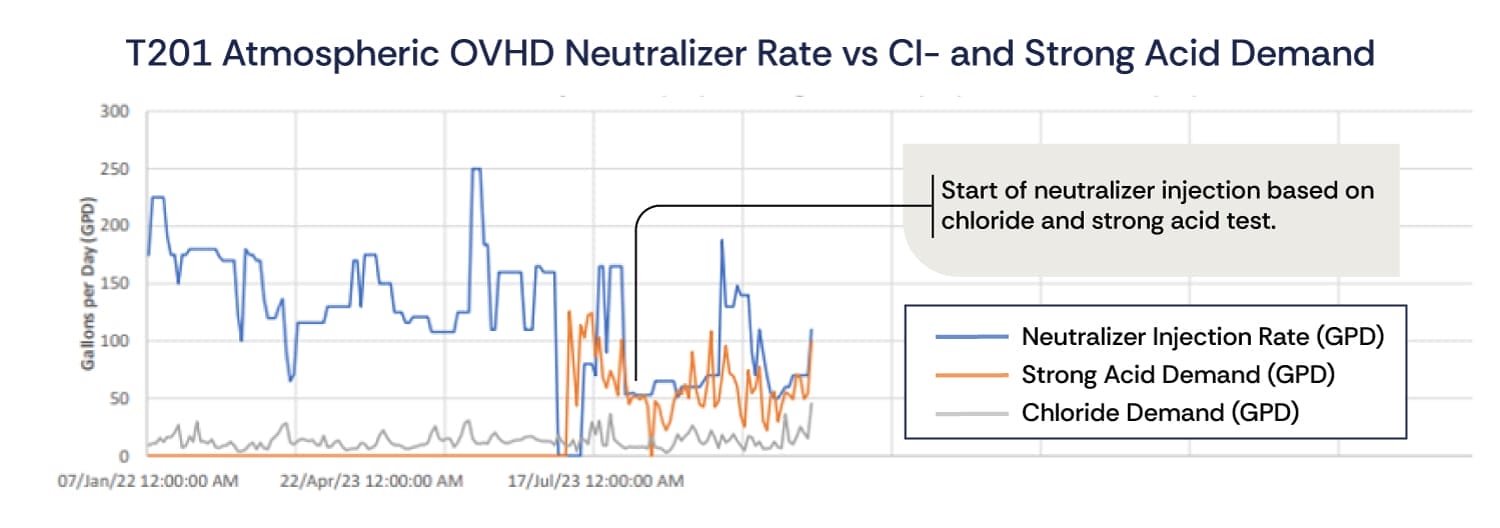
Cost Savings: The neutralizer’s average daily treatment cost has decreased, resulting in an annualized savings of approximately $500,000.